14 Key Mechanical Properties of Wood: Strength Properties Explained
Having worked with wood for over a decade, I’ve seen first-hand the pivotal role its mechanical properties play. From the ancient shipyards to modern homes, wood’s unique attributes have cemented its position as an indispensable material. Its blend of strength, elasticity, and aesthetic appeal is unmatched, which explains its continued prominence in both traditional and modern applications.
There’s a marvel in the diversity of over 73,000 tree species. Every forest trip I’ve embarked upon brought me face-to-face with woods, each with unique textures, grains, and strengths. Be it the dense Oak forests of Europe or the lightweight Balsa trees of Central America; each wood speaks of its own unique mechanical narrative.
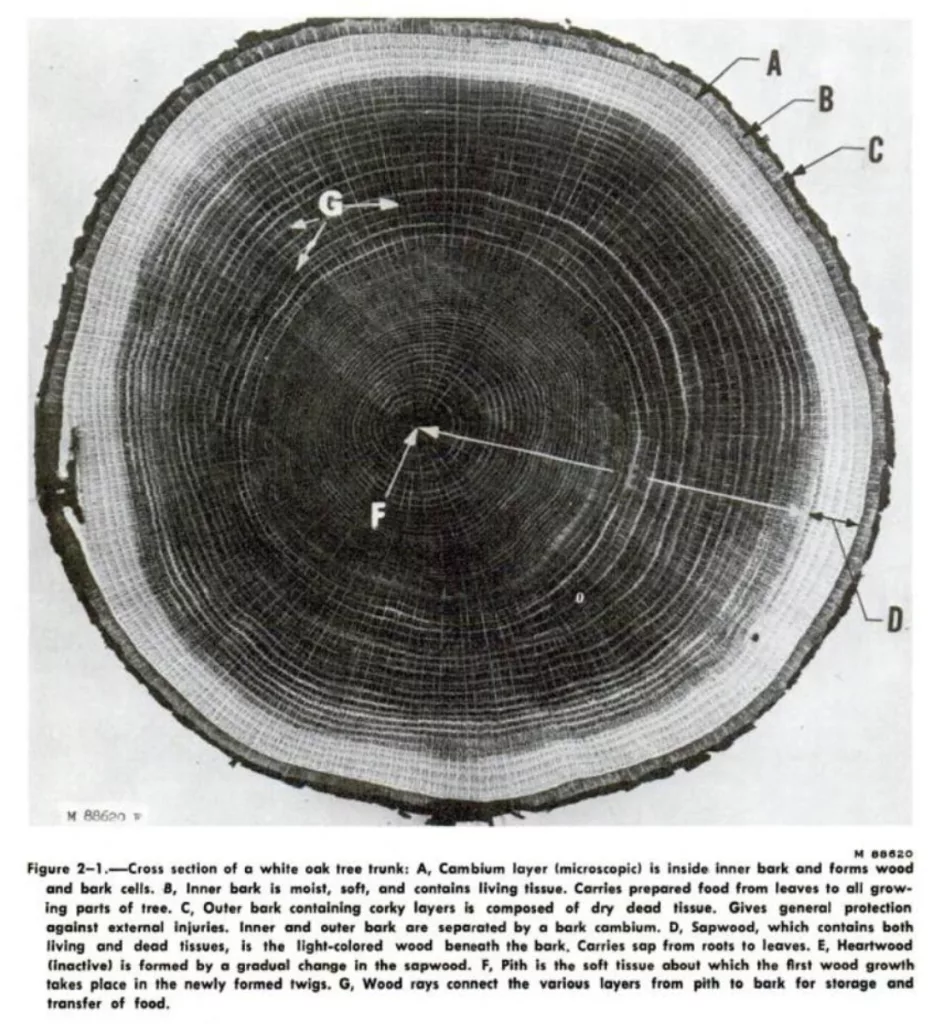
Key Mechanical Properties of Wood Explained
Before starting the discussion on certain properties involving mechanical strengths of the timber, I should tell a few things. The mechanical attributes of wood determine its behavior under various stresses, playing a pivotal role in its suitability for diverse applications in construction and design. These intrinsic characteristics, influenced by species, moisture content, and grain orientation, guide engineers and craftsmen in selecting the appropriate wood for specific tasks.
Following are the three principal axes of wood with respect to grain direction and growth rings. All the forces discussed here will have relation with these axes.

Density (It is Also a Physical Property)
During my years working in the field, I’d often pick up a wood sample and its weight would narrate its story. Dense woods, like Ebony with a density of around 1,200 kg/m^3, often promise strength and resilience, making them apt for heavy-duty constructions. When assessing the suitability of wood and wood products for specific purposes, the density of dry wood is a significant factor to consider. I have discussed this parameter in the physical properties of wood.
Variations in Density Across Wood Species
Each forest region showcases its gallery of wood densities:
Wood Type | Average Density (kg/m³) |
---|---|
Pine | 500 – 700 |
Oak | 600 – 900 |
Cedar | 370 – 580 |
Mahogany | 500 – 850 |
Maple | 600 – 750 |
Cherry | 580 – 630 |
Teak | 630 – 720 |
Birch | 600 – 700 |
Redwood | 450 – 510 |
Walnut | 610 – 700 |
Spruce | 400 – 700 |
Fir | 450 – 510 |
Ash | 650 – 850 |
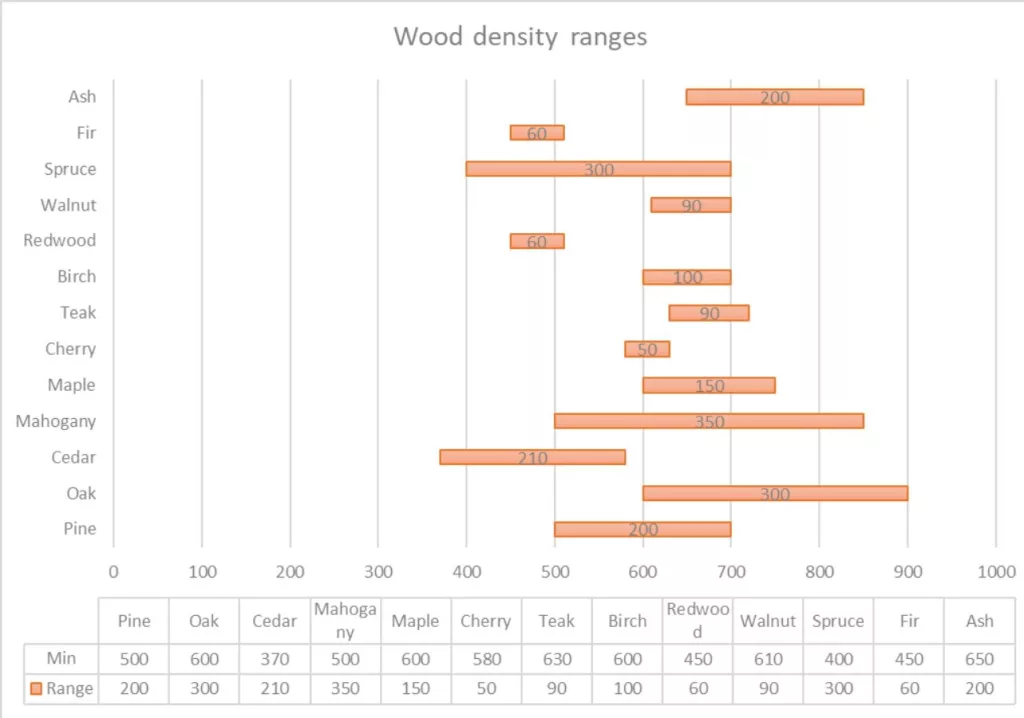
Tensile Strength
Tensile strength (Resisting Stretching Forces), also known as tension strength, measures a wood material’s ability to withstand loads that tend to elongate it. Different woods have varying tensile strengths based on their species, grain orientation, and moisture content of the wood. The tensile stress parallel to the grain is often higher than that perpendicular to the grain, highlighting wood’s anisotropic nature.
Here are the approximate tensile strength values for some common woods:
Wood Type | Tensile Strength (MPa) |
---|---|
Douglas Fir | 40 – 75 |
Oak (Red) | 50 – 83 |
Pine (Yellow) | 35 – 70 |
Hickory | 75 – 105 |
Maple (Hard) | 55 – 92 |
Teak | 50 – 80 |
Bamboo | 100 – 350 (based on species and processing) |
During a workshop, I once tested the tensile strength of Hickory – a wood renowned for its resilience. It resisted forces beyond my expectations, explaining its use in tool handles and sports equipment. One more thing, clear wood has a higher tensile strength, especially when the forces are applied parallel to the grain. The uninterrupted fibers contribute to its ability to resist stretching without breaking.
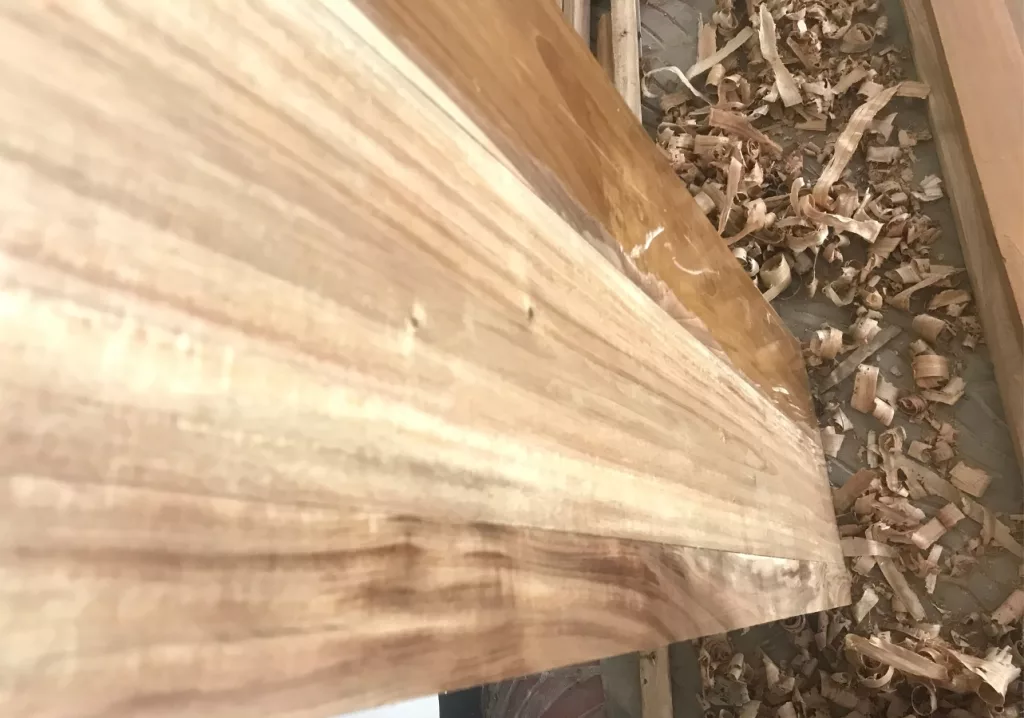
In the forests of Asia, I once saw bamboo structures enduring immense weights, revealing a live demonstration of wood strength. Strength properties are important field of study to know if you like to make wood crafts. Wood and wood-based materials are not something that you choose randomly.
Compressive Strength
I’ve often noticed Douglas Fir used in vertical beams in buildings. With its impressive compressive strength due to its parallel grain direction, it stands tall and unyielding. The compressive or crushing strength of wood is a vital factor when considering its use in load-bearing applications.
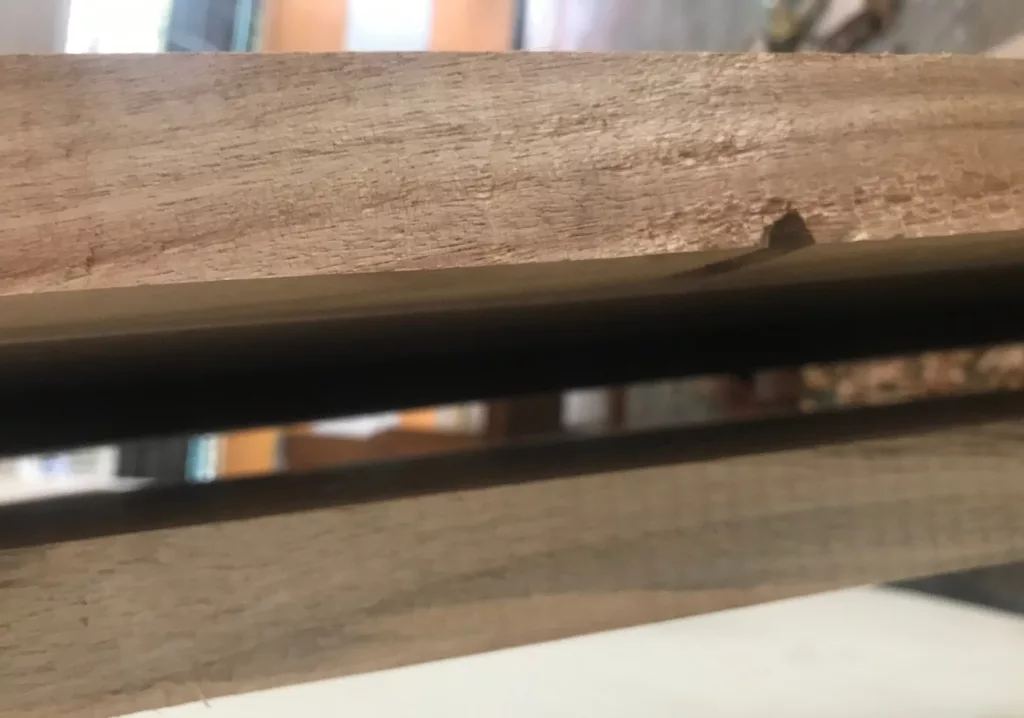
Compressive strength measures the ability of a material to resist forces pushing it together, or compressive forces. In the context of wood, compressive strength is usually measured along the grain because wood is much stronger in this direction. Here are approximate compressive strength values for some common woods:
Table: Compressive Strength of Common Woods (Parallel to Grain)
Wood Type | Compressive Strength (MPa) |
---|---|
Douglas Fir | 42 – 55 |
Oak (Red) | 40 – 60 |
Pine (Yellow) | 30 – 48 |
Hickory | 50 – 66 |
Maple (Hard) | 54 – 62 |
Teak | 37 – 55 |
Beech | 50 – 62 |
Flexural Strength or Modulus of Rupture
Craftsmen value woods like Ash for their flexural strength. I recall designing a curved chair back, and Ash’s ability to bend without compromising its integrity was remarkable.
Flexural strength, often referred to as the modulus of rupture, describes the ability of a material to resist deformation under load. It’s particularly crucial for understanding how wood will behave when subjected to bending forces. The modulus of rupture in bending is an essential metric in testing the performance. Transverse or bending strength plays a critical role when wood is used in beams or arches.
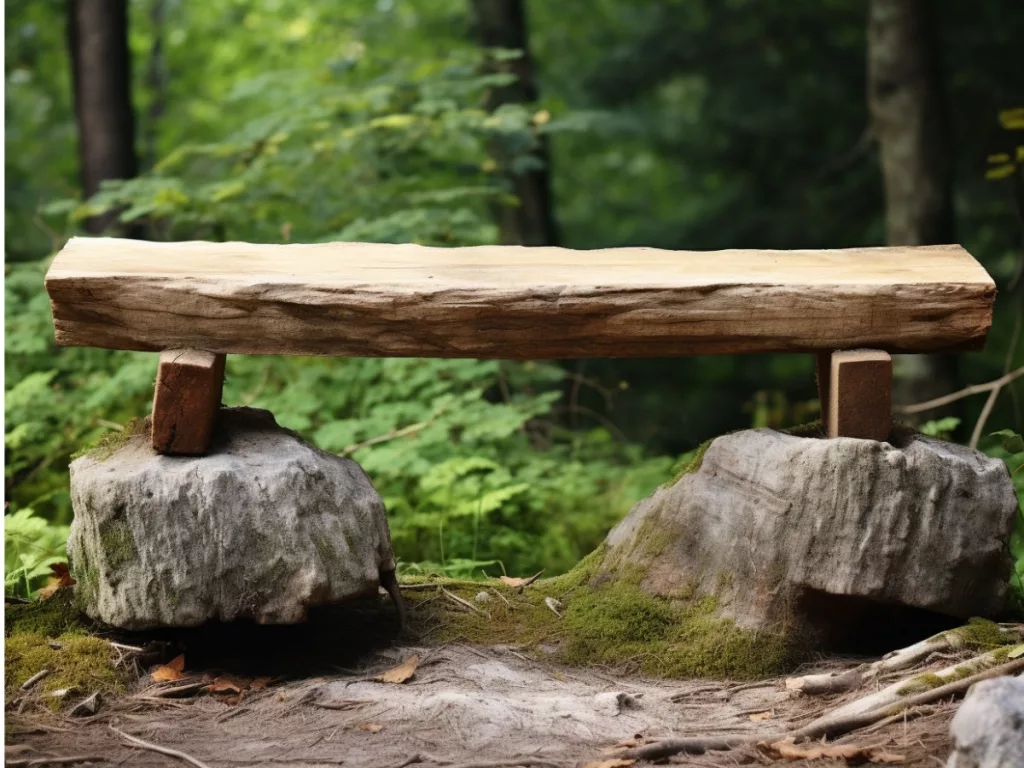
In the context of wood and many other materials, “Flexural Strength” and “Modulus of Rupture” are synonymous terms. They both represent the maximum stress a material can withstand when bent before breaking. Here are approximate values for the modulus of rupture or flexural strength of some common woods:
Table: Flexural Strength (Modulus of Rupture or MOR) of Common Woods
Wood Type | Flexural Strength (MPa) |
---|---|
Douglas Fir | 80 – 105 |
Oak (Red) | 90 – 120 |
Pine (Yellow) | 70 – 90 |
Hickory | 100 – 130 |
Maple (Hard) | 85 – 110 |
Teak | 75 – 100 |
Beech | 85 – 115 |
In an experiment with Beech wood, known for its robust modulus of rupture, it withstood significant stress, making it clear why it’s a preferred choice for load-bearing structures.
Torsional Stiffness
This property counteracts the twisting of wood. A high torsional stiffness, measured in Modulus of Rigidity (psi), indicates that the wood can resist warping or twisting effectively.
Significance: Ensuring that wood has adequate torsional stiffness is essential when it’s used in structural components like beams or shafts. These elements need to retain their shape under external forces.
Wood Type | Modulus of Rigidity (psi) |
---|---|
Red Oak | 2.2 million |
White Oak | 1.03 million |
Pine | 1 million |
Red Maple | 2.2 million |
Birch | 1.3 million |
Douglas Fir | 1.2 million |
Red Cedar | 900,000 |
Walnut | 1.3 million |
Cherry | 1.25 million |
Teak | 1.1 million |
Ash | 1.35 million |
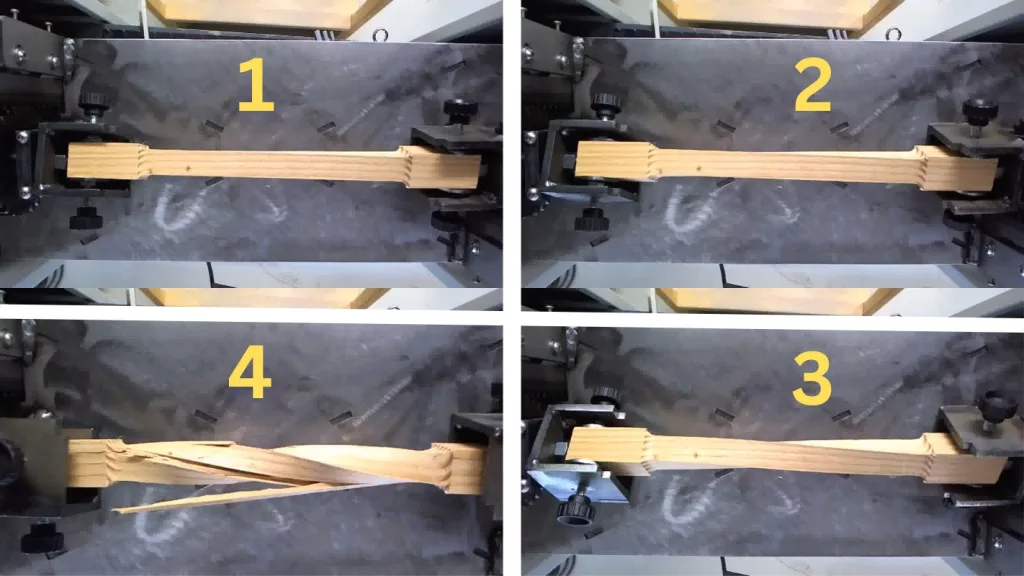
Moritz Sanne)
I can relate a brilliant example from my childhood, the distinct difference in torsional rigidity between woods became evident when I made spinning tops. An oak top maintained its spin brilliantly, showcasing oak’s impressive torsional rigidity. On the other hand, a pine top didn’t fare as well, a reflection of its softer nature.
Hardness
It is Resistance Against Wear and Indentation. On a trek through Brazil, I chanced upon Ipe wood. When I tried indenting its surface with a key, it stood unscathed – a testament to its high Janka hardness rating of over 3,500 lbf.
Hardness in wood defines its ability to resist dents, scratches, and wear. I will discuss about Janka hardness separately in detail. Hardness is one of the key surface and interactional properties. We will have a separate discussion on this very crucial property.
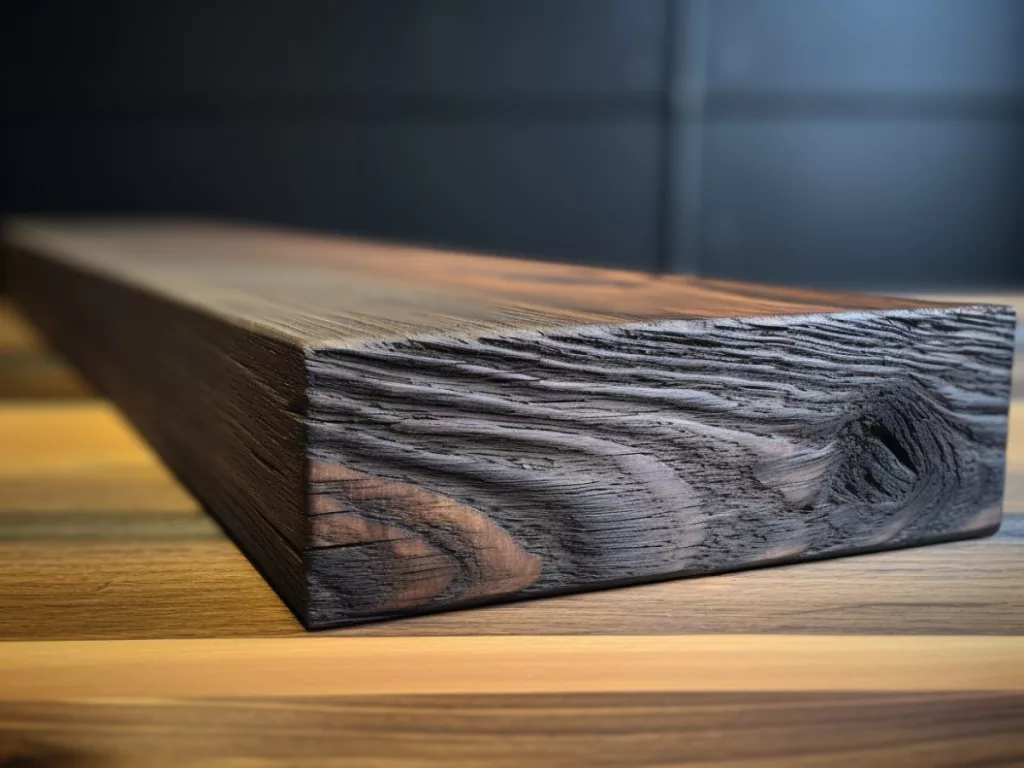
Shear Strength
Shear strength of wood refers to the ability of a material to resist forces that cause internal layers of the material to slide against each other. For woods, this strength is particularly crucial when considering joinery, since connections like mortise and tenon or dowel joints rely heavily on wood’s shear strength.
Here are approximate shear strength values (parallel to the grain) for some common woods:
Table: Shear Strength of Common Woods (Parallel to Grain)
Wood Type | Shear Strength (MPa) |
---|---|
Douglas Fir | 8 – 12 |
Oak (Red) | 10 – 15 |
Pine (Yellow) | 6 – 10 |
Hickory | 10 – 15 |
Maple (Hard) | 9 – 13 |
Teak | 7 – 11 |
Beech | 8 – 12 |
In joinery, the Mahogany’s commendable shear strength is a craftsman’s dream, ensuring joints hold together seamlessly.
Cleavage Strength
This is the ability to Prevent Splits and Cracks. Cleavage strength is especially relevant when considering the potential for wood to split, particularly during nailing, screwing, or when subjected to forces perpendicular to the grain. This property is closely related to the wood’s ability to resist splitting along its grain. While shear strength pertains to sliding forces parallel to the grain, cleavage strength deals with forces attempting to split the wood apart perpendicular to the grain.
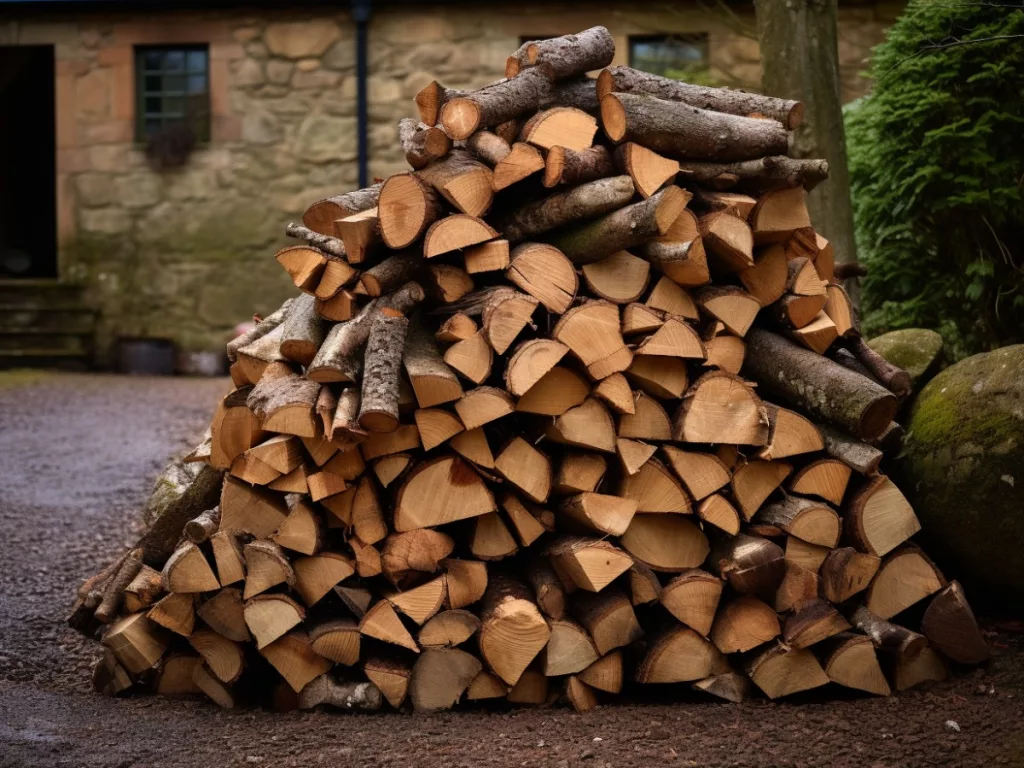
Unfortunately, cleavage strength is not as commonly referenced as some of the other mechanical properties like shear or tensile strength.
Table: Cleavage Strength of Common Woods (Perpendicular to Grain)
Wood Type | Cleavage Strength (MPa) |
---|---|
Douglas Fir | 1 – 3 |
Oak (Red) | 3 – 5 |
Pine (Yellow) | 1.5 – 3 |
Hickory | 3 – 5 |
Maple (Hard) | 2 – 4 |
Teak | 2 – 4 |
Beech | 2 – 4 |
Red Oak, despite its strength, has a moderate cleavage strength. This property became evident when I was once splitting logs for a winter project.
Coefficient of Friction
The coefficient of friction (CoF) is a measure of how much resistance there is to sliding between two surfaces in contact. For wood, the CoF can be essential for understanding its “grip,” especially when it’s used for flooring, decking, or any application where slippage could be a concern.
The coefficient of friction for wood can vary based on numerous factors including the species of wood, the surface finish (e.g., polished, rough, coated with a certain finish), the type of object in contact with the wood, and the presence of any contaminants like water, oil, or dust.
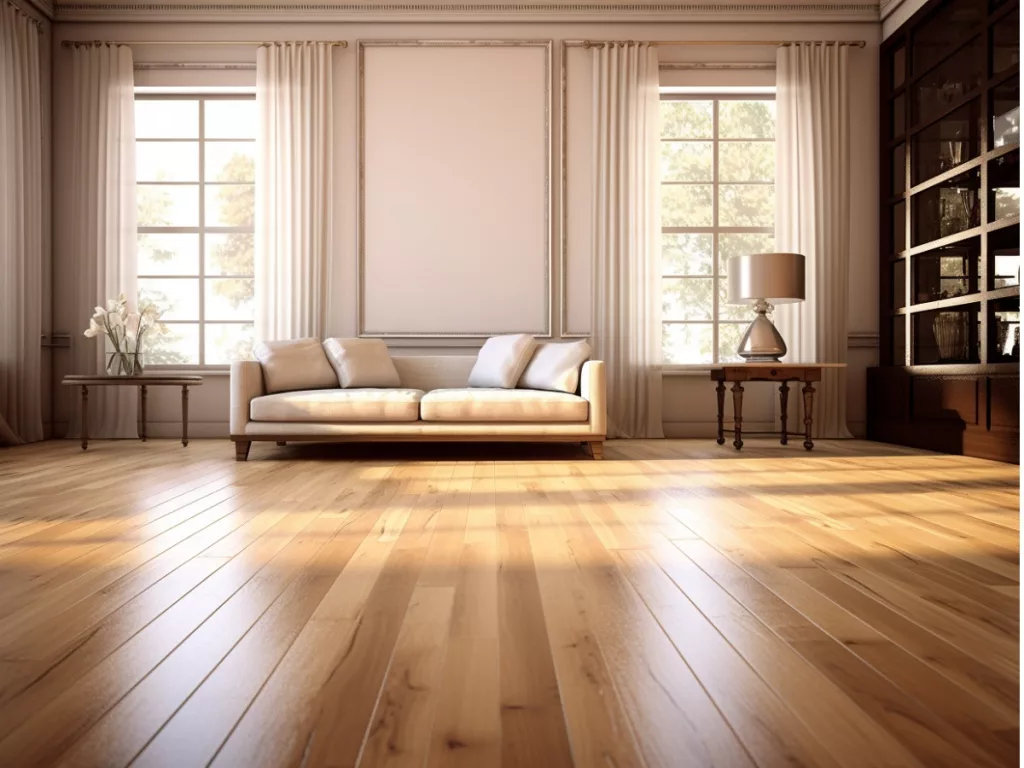
Here are some approximate values for the static coefficient of friction of common woods against common materials:
Table: Static Coefficient of Friction for Common Woods against Various Materials
Wood Type | CoF with Rubber | CoF with Dry Steel | CoF with Wet Steel |
---|---|---|---|
Oak (Red) | 0.62 | 0.50 | 0.35 |
Pine (Yellow) | 0.58 | 0.48 | 0.32 |
Maple (Hard) | 0.60 | 0.51 | 0.34 |
Teak | 0.59 | 0.49 | 0.33 |
Beech | 0.61 | 0.50 | 0.34 |
Note: These values are illustrative and approximate. Actual CoF can vary widely based on the exact conditions, specific samples, and testing methods.
When considering these values in real-world applications, remember that environmental conditions can play a significant role. For instance, a wet wood or oily wood surface will typically have a much lower CoF, leading to increased slipperiness.
Teak, often used for boat decks, offers an impressive grip even when wet, showcasing its optimal coefficient of friction.
During a woodworking workshop, I handled various wooden boards. The red oak’s natural grip was evident when sliding a rubber-soled shoe across it, showing its high coefficient of friction. In contrast, a smoother pine board was noticeably more slippery, highlighting the importance of wood type in slip resistance.
Stiffness and the Modulus of Elasticity
Mechanical features of wood considered in design include not just compressive and tensile strengths, but also shear, torsional, and modulus of elasticity. Tests on the strength and modulus of elasticity are critical for finding the material’s mechanical behavior.
In simpler terms, Modulus of Elasticity (often referred to as the wood’s stiffness) describes how much a piece of wood will deform under a certain load before it begins to permanently bend or break. The MOE is typically measured in pascals (Pa) or its multiples like megapascals (MPa) or gigapascals (GPa). Higher values indicate stiffer, less flexible wood, while lower values indicate more flexible wood.
Table: Stiffness and Modulus of Elasticity (MOE) of Common Woods
Wood Type | Modulus of Elasticity (GPa) |
---|---|
Douglas Fir | 12 – 14 |
Oak (Red) | 11 – 13 |
Pine (Yellow) | 8 – 12 |
Hickory | 14 – 16 |
Maple (Hard) | 12 – 15 |
Teak | 10 – 13 |
Beech | 11 – 14 |
Note: These values are approximate averages. Actual MOE can vary depending on growth conditions, age of the wood, moisture content, and other factors.
Here’s a video you will like to watch on this.
I recall testing the stiffness of wood samples, taken the pieces of wood from a pile of logs. The hickory always stood out; its high modulus of elasticity made it noticeably stiffer than others, a characteristic crucial for certain tool handles and sports equipment. Conversely, while working with pine, its relative flexibility compared to hickory was evident, making it more suitable for applications requiring a bit of give.
Using Maple for crafting musical instruments was a revelation. Its stiffness ensures that the instruments hold their tune and produce melodious sounds.
Toughness
Toughness represents a material’s capacity to absorb energy up to the point of fracturing. Toughness of wood can vary significantly based on factors like moisture content, grain direction, temperature, and wood species. Generally, tougher woods are preferable for applications where the material might experience impact or sudden stresses.
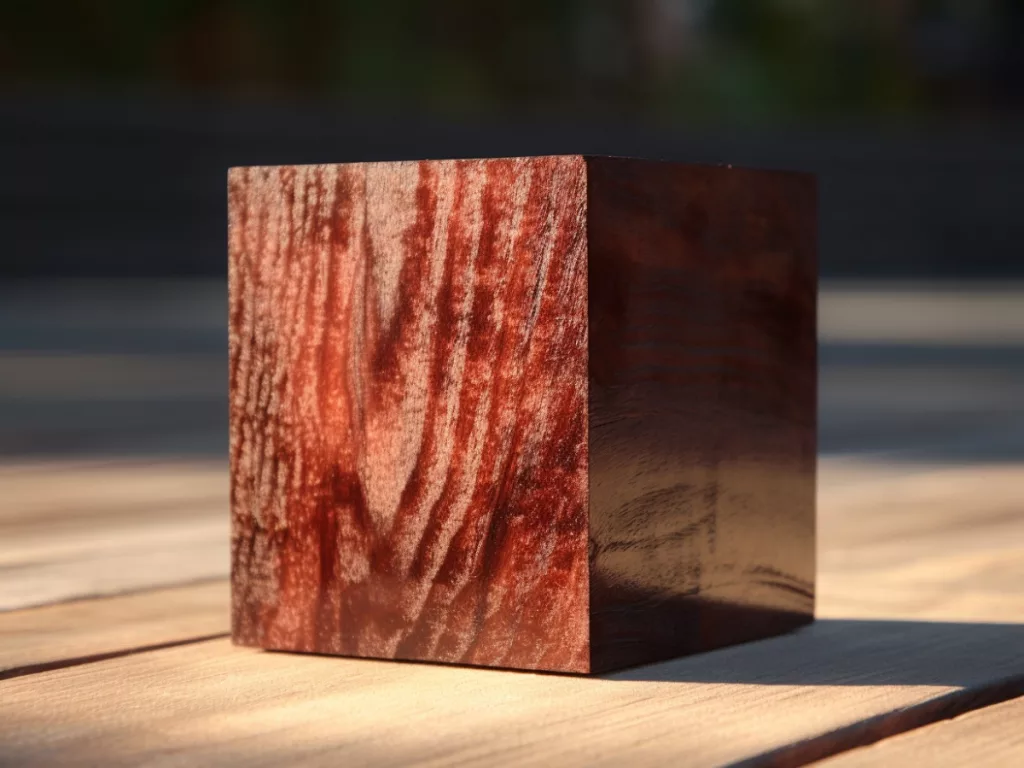
This video illustrates greatly on this toughness.
Table: Approximate Toughness Values for Common Woods
Wood Type | Toughness (J/m^3) |
---|---|
Douglas Fir | 5,500 – 6,500 |
Oak (Red) | 6,300 – 7,400 |
Pine (Yellow) | 4,800 – 5,600 |
Hickory | 7,200 – 8,400 |
Maple (Hard) | 5,900 – 7,000 |
Note: These values are broad approximations. Real-world toughness can fluctuate based on testing methods, growth conditions, and wood treatment.
Examples
Hickory
Often chosen for tool handles, such as axes and hammers, due to its high toughness. It can absorb significant energy from impacts without fracturing easily. Having witnessed a baseball bat manufacturing unit, the choice of Hickory and Ash, woods that exemplify toughness, became apparent as they resisted shattering impacts.
Pine
While pine has moderate toughness, it’s not as tough as hickory. If used for an application like a tool handle, it might not withstand repetitive high-energy impacts as effectively.
I vividly recall a test where we compared the toughness of different woods. Using an impact testing machine, we applied sudden forces to small wood samples. Hickory consistently outperformed most woods, resisting fractures remarkably well under impact.
Conversely, softer woods like pine, while still exhibiting decent toughness, showed signs of damage more quickly. This experiment highlighted the importance of choosing the right wood for applications that are prone to sudden stresses or impacts.
Elasticity vs. Plasticity: The Balance of Deformation
Elasticity (defines pliability of the wood) and plasticity describe how materials deform under stress. When a material is loaded and it returns to its original shape upon unloading, this behavior is termed “elastic.” If the material does not return to its original shape and has permanent deformation, this behavior is termed “plastic.”
In the context of wood, it’s essential to understand that wood is primarily elastic under normal conditions. Permanent deformation, or plastic behavior, usually occurs when the wood is overloaded beyond its elastic limit.
Table: Elastic and Plastic Deformations in Common Woods
Wood Type | Elastic Deformation Range (%) | Plastic Deformation Range (%) |
---|---|---|
Douglas Fir | 0.1 – 0.5 | >0.5 – 1.5 |
Oak (Red) | 0.1 – 0.6 | >0.6 – 1.7 |
Pine (Yellow) | 0.1 – 0.7 | >0.7 – 2.0 |
Hickory | 0.1 – 0.4 | >0.4 – 1.4 |
Maple (Hard) | 0.1 – 0.5 | >0.5 – 1.6 |
Spruce, often used in aircraft construction, showcases a blend of elasticity and plasticity, making it resilient yet flexible.
Examples
- Elasticity: Wooden floorboards in old houses might creak and slightly deform underfoot. But once the weight is lifted, they return to their original position due to their elastic nature.
- Plasticity: A bookshelf made of softwood might sag over time if overloaded with books. This sagging is a result of the wood undergoing plastic deformation, wherein it doesn’t return to its initial shape after the stress is removed.
Workability: Crafting with Ease
Workability refers to how easily a wood can be cut, shaped, machined, and finished. This is a crucial factor for woodworkers, craftsmen, and manufacturers, as certain woodworking tasks require woods with particular workability characteristics. Workability variables given below:
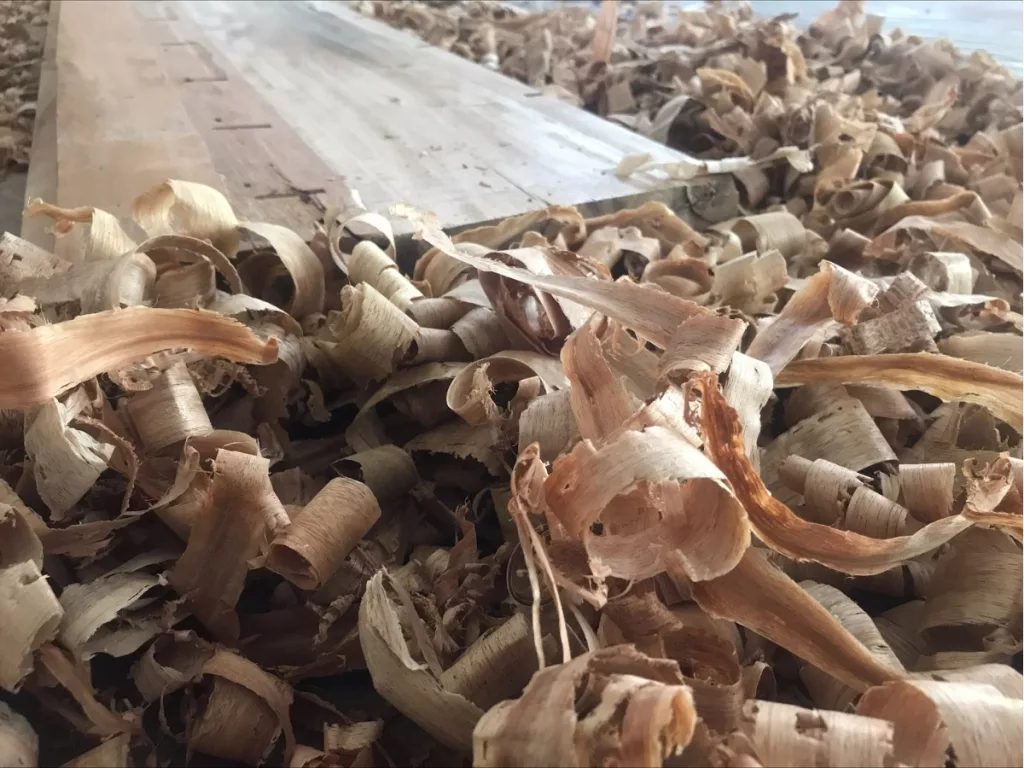
- Influenced by wood’s density, grain pattern, moisture content, and natural resins.
- Determines ease of cutting, drilling, planing, and carving.
- Impacts the finish quality after staining or painting.
- Certain woods can dull cutting tools faster due to high silica content or hardness.
Table: Approximate Workability Values for Common Woods
Wood Type | Workability (Scale 1-10; 10 being easiest) |
---|---|
Douglas Fir | 8 |
Oak (Red) | 6 |
Pine (Yellow) | 9 |
Hickory | 5 |
Maple (Hard) | 7 |
Note: This scale is a subjective representation based on general woodworking feedback. Actual workability can vary based on tools used and individual wood samples.
Examples
- Pine (Yellow): Its high workability score makes it a favorite among beginners in woodworking. It’s easy to cut, carve, and shape, making it ideal for DIY projects or in any kind of household/commercial use of wood.
- Hickory: While incredibly tough and durable, hickory’s lower workability score indicates it can be a bit more challenging to work with. It requires sharper tools and more effort to achieve a smooth finish. You will find less hickory wood products for daily use, particularly if it is not a structural timber.
During a woodworking workshop I conducted, the choice of wood became the centerpiece of a lively discussion. We worked with both pine and hickory. The participants, mostly novices, found the pine more forgiving and easier to shape into their desired crafts.
In contrast, working with hickory demanded more patience and precision, often requiring multiple attempts to achieve the desired outcome. This experience underlined the importance of wood selection, especially when catering to craftsmen of varying skill levels.
From my experience, Pine stands out when it comes to carving intricate designs, highlighting its unparalleled workability.
Ductility and Brittleness
Ductility in general refers to the bending strength of any material. This behavior depends on the porosity, fiber density and the overall structure of wood. A nice video on ductility is here for your understanding.
When it comes to wood, “ductility” and “brittleness” aren’t standard mechanical properties measured in the same way as metals or polymers. Instead, woods are typically described in terms of their tensile strength, modulus of elasticity, and failure characteristics.
However, certain woods can demonstrate behaviors that we might colloquially described as more “brittle” (i.e., they break without much deformation, and this is a material that is difficult to bend) or more “ductile” (i.e., they deform more before breaking).
Brittle wood which gives way are never trusted for any load carrying structure. And the energy stored in the material is released easily if it is brittle. But this weakness does not play any role in use of wood for floors.
Since there aren’t direct measures of ductility and brittleness for wood as there are for metals, I can provide a general categorization based on their tensile behavior:
Table: Relative Ductility and Brittleness of Common Woods
Wood Type | Relative Behavior |
---|---|
Douglas Fir | Moderately Ductile |
Oak (Red) | Moderately Ductile |
Pine (Yellow) | Ductile |
Hickory | Brittle |
Maple (Hard) | Moderately Brittle |
Teak | Ductile |
Beech | Moderately Ductile |
I remember assessing the tensile behavior of woods in a lab at my university. Pine, with its relatively ductile nature, could endure more stretching before breaking, making it an intriguing choice for certain craft projects. In contrast, hickory’s brittleness was evident when subjected to tensile forces; it broke with minimal deformation. Observing craftsmen at work, Yew’s ductility became evident as it was molded into slender, elongated forms without snapping. I
Examples
Ductility: Pine, known for its relatively ductile behavior, is often used for wooden toys. When these toys are subjected to forces, they can slightly deform without immediately breaking, ensuring a longer lifespan of the toy.
Brittleness: Hickory, due to its brittleness, is chosen for applications where a sudden, clean break is preferable, such as certain tool handles. In case of over-stress, a hickory handle would break cleanly, potentially preventing more significant damage or injury.
Clear Wood Properties
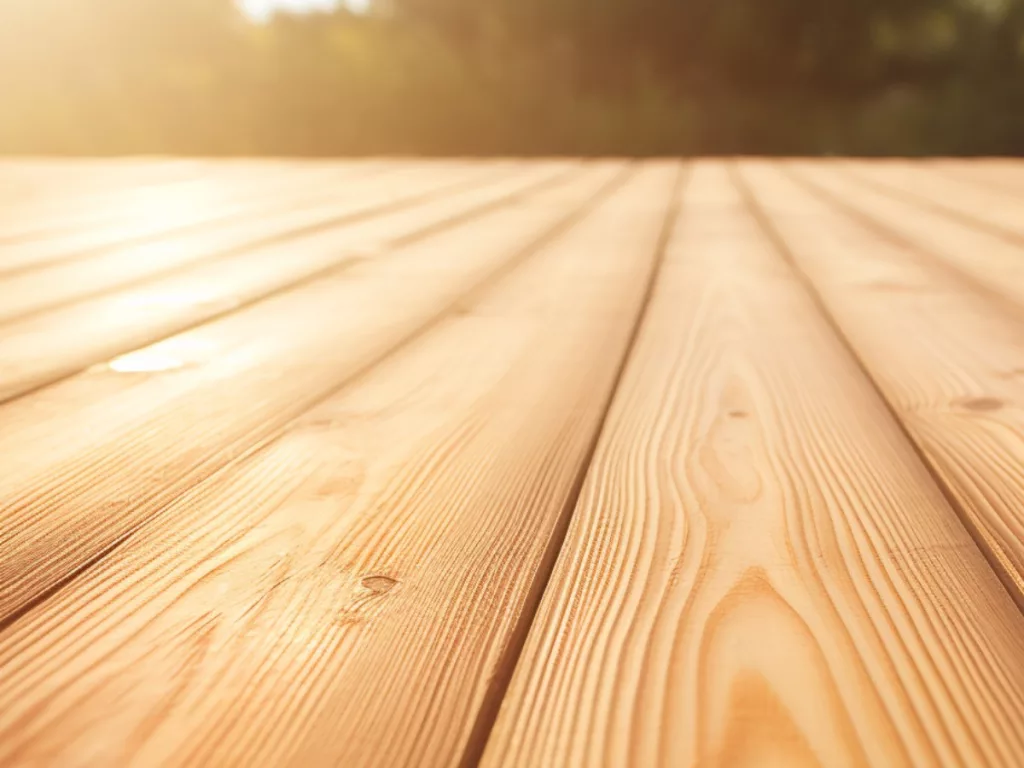
Clear wood properties refer to the characteristics of wood that are devoid of defects such as knots, checks, and other imperfections. These properties are essential for understanding the inherent qualities of the wood species without the influence of natural or growth-related defects. Let’s recall the properties again while watching this –
Here are some of the properties:
- Uniform Appearance: Clear wood is free from visible defects like knots, which results in a consistent and predictable appearance.
- Higher Strength: Without defects, clear wood tends to exhibit higher mechanical strengths compared to non-clear wood of the same species.
- Predictable Behavior: The absence of defects means that the wood will behave more uniformly when subjected to stresses or during machining.
- Premium Quality: Clear wood is often considered premium quality due to its flawless appearance and is thus preferred for fine woodworking or decorative purposes.
- Ease of Finishing: With a uniform grain and absence of defects, clear wood accepts finishes more evenly, resulting in a smoother and more polished look.
- Stability: Clear wood is often more stable in response to environmental changes since defects can sometimes be points of vulnerability to moisture uptake or differential shrinkage.
- Desirability in Crafting: For intricate crafts or detailed work, the predictability of clear wood makes it a favored choice.
- Higher Cost: Due to its desirability and premium nature, clear wood often comes at a higher price point than other types of wood.
Some Key Points You Should Know
- Clear wood, being free of defects such as knots, checks, and pitch pockets, often exhibits superior mechanical strengths in comparison to its knotty counterpart. Clear wood specimens are often used in mechanical tests to accurately gauge the inherent strengths of a timber species.
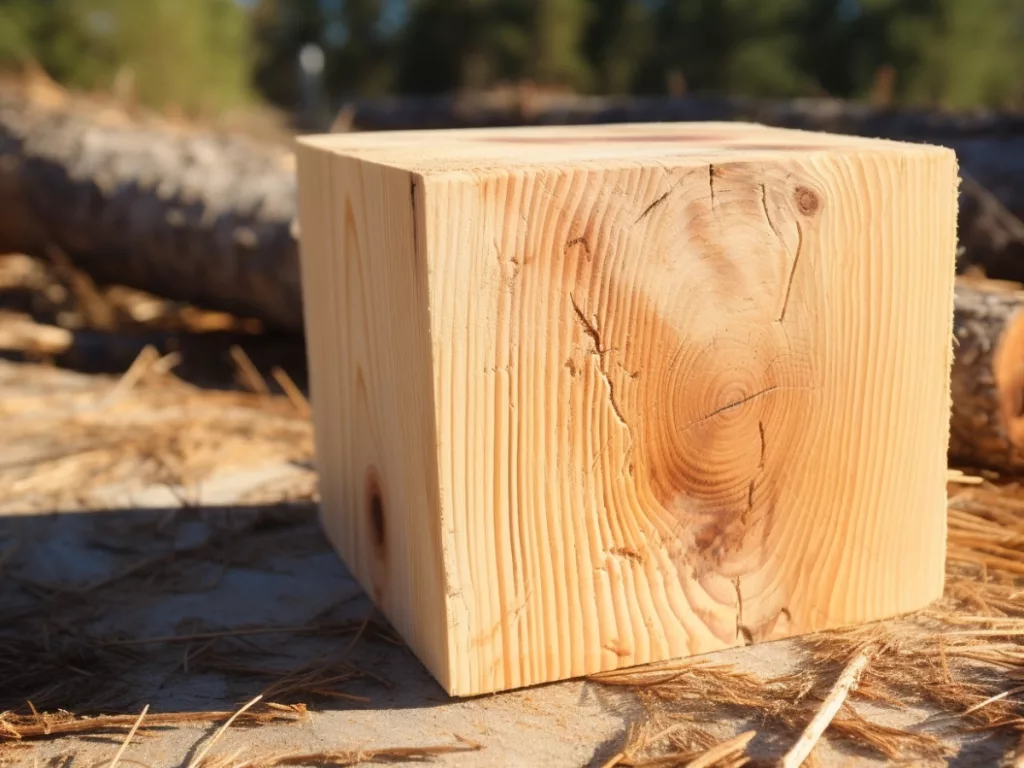
- Early wood, also referred to as “springwood,” is the portion of the growth ring in a tree that forms at the beginning of the growing season. Because of its structure, early wood is generally less dense and has lower mechanical strength compared to latewood.
- The strength parallel to the grain is a crucial consideration when selecting wood for structural beams, as it directly influences the beam’s ability to support loads without failing.
Let’s take a break and watch this video on choosing your preferred timber.
- The mechanical properties of the wood and the strength of timber, being parts of wood science, dictate its suitability for various construction projects.
- The design of timber structures requires a comprehensive understanding of wood’s mechanical and physical properties.
- The testing of wood is essential to ensure its quality and suitability for specific applications.
- Knowledge of the mechanical properties is fundamental for making informed decisions in woodworking. This understanding guarantees the wood’s appropriate use in construction and other applications.
- Any wood meant to be used in structures and load carrying functions must go under a the mechanical properties tests. A thorough knowledge of these tests on the strength ensures that the wood’s mechanical properties are well-understood.
- The method by which wood is dried can significantly influence the mechanical properties of the material. Temperature on wood plays a crucial role in determining its strength. Oven-dry wood often exhibits different characteristics compared to naturally seasoned timber.
- Assessing how various factors, such as load on the strength, affect the overall strength of a beam or column is vital.
- One must remember that wood is an orthotropic material, with distinct properties in different directions. Wood parallel to the grain often exhibits superior mechanical properties due to its aligned fibers.
- The dimensions of the wood elements, such as thickness and width, can influence its strength and flexibility.
- When wood is subjected to stress, its response varies based on its moisture content, species, and orientation.
Conclusion
My journey as a wood enthusiast has ingrained in me a deep appreciation for this renewable resource. From the craftsman’s workshop to grand architectural marvels, selecting the right wood ensures a blend of aesthetics, durability, and purpose. Understanding wood’s mechanical properties is akin to understanding nature’s symphony, where every tree plays its unique note. The Forest Service plays a pivotal role in managing and preserving vast tracts of woodland for both ecological balance and public recreation. Next time you pay a visit to any national park, say “Hello!” to the forest service person as what a treasure he or she is caring for.
Related Read
References
- Bodig, J., & Jayne, B. A. (1982). Mechanics of Wood and Wood Composites, ISBN-13 : 978-0894647772
- Forest Products Laboratory. (1999). Wood Handbook: Wood as an engineering material, ISBN-13: 978-1484859704
- D. E. Breyer. (2007). Design of Wood Structures—ASD/LRFD, ISBN-13: 978-1260128673
FAQs
What are the mechanical properties of wood?
Wood has various mechanical properties such as strength, bending strength, shear strength, compressive strength, and tensile strength. These properties determine the ability of wood to withstand different types of forces and loads.
How does wood bend?
Bending is a property of wood that allows it to deform under the action of an applied force. Wood can bend due to its inherent flexibility and the arrangement of cellulose fibers within its structure.
What is the role of the Forest Service in relation to wood?
The Forest Service is an organization responsible for managing and protecting forests. They play a vital role in ensuring sustainable wood production, forest conservation, and promoting the use of wood as a renewable resource.
What is tensile strength?
Tensile strength is the ability of wood to resist being pulled apart when subjected to tension or stretching forces. It is an important property in applications where wood is exposed to pulling or stretching forces.
What is the strength of wood?
The strength of wood refers to the overall ability of wood to withstand loads and forces without breaking, all are mechanical properties. It encompasses various strength properties such as bending strength, compressive strength, tensile strength, and shear strength.
What is structural timber?
Structural timber refers to wood that is specifically designed and graded for use in construction and structural applications. It is commonly used in building frameworks, beams, columns, and other load-bearing structures.
What are wood products?
Wood products refer to various materials and items made from wood or wood-based materials. Examples include furniture, flooring, doors, windows, plywood, particle board, and many other products used in construction, interior design, and everyday applications.
What are the mechanical properties of timber in construction?
Here are the mechanical properties of timber in construction:
Compressive Strength
Tensile Strength
Flexural Strength (Modulus of Rupture)
Shear Strength
Hardness
Toughness
Stiffness (Modulus of Elasticity)
Ductility and Brittleness
Durability
Workability